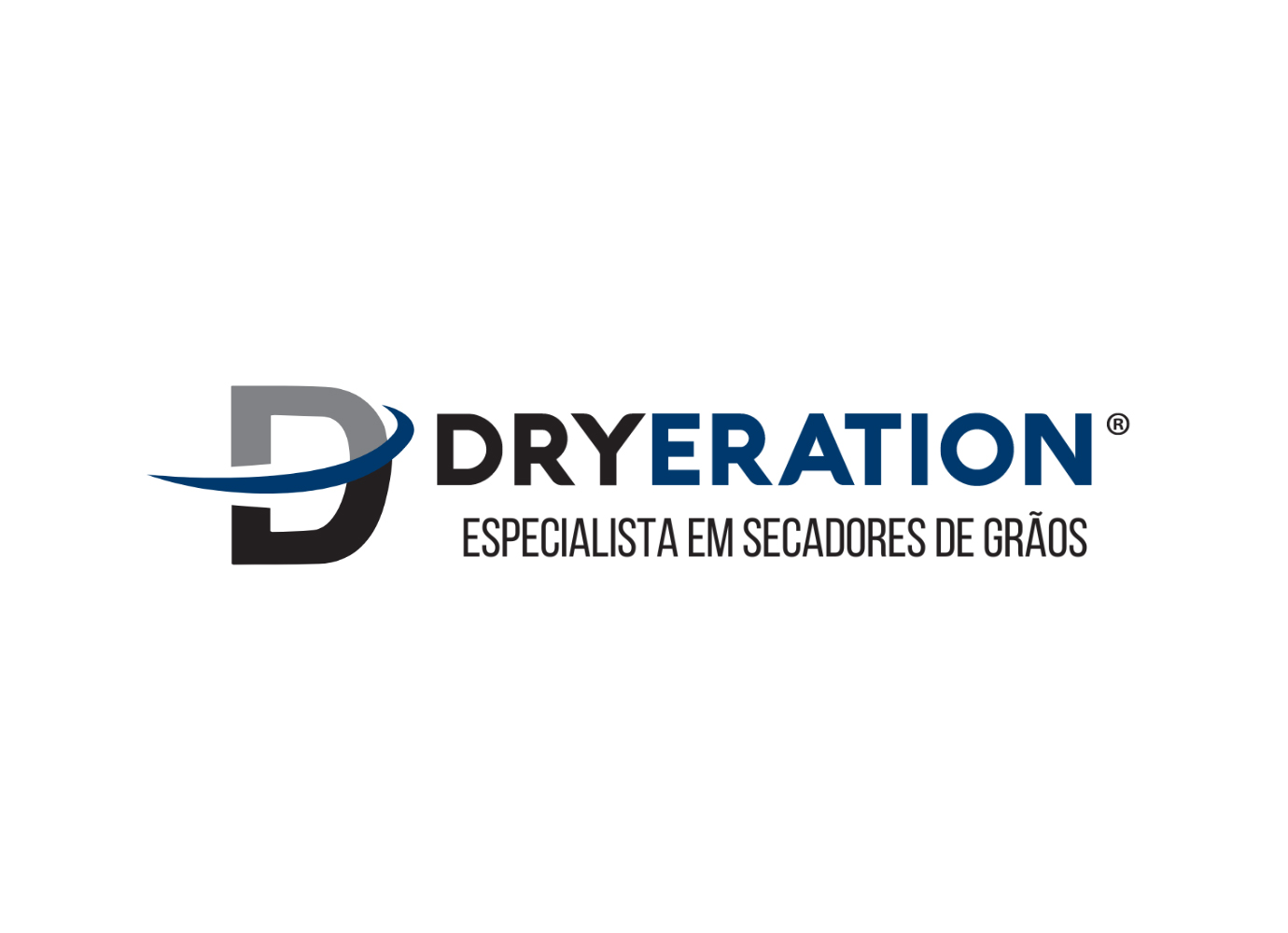
27 jan MELHORES PRÁTICAS – Colheita
MEHORES PRÁTICAS – Colheita
INTRODUÇÃO
Para atender a demanda pelo crescimento de área plantada e produtividade da agricultura brasileira as colheitadeiras evoluíram juntas com o trator devido a oferta de maiores potências dos motores, mas de forma geral tiveram significantes evoluções:
- Devido ao plantio direto a necessidade de ter plataformas de corte flexível na década de 70;
- Maiores tamanhos nas décadas seguintes, incluindo as Classes 5 e 6;
- Cabina pressurizada e climatizada, na década de 80;
- Sistema de Trilha Axial na década de 90;
- Agricultura de Precisão e Tração Traseira Auxiliar da década 2000;
- Plataforma Drapper na década de 2010;
- Sistemas de debulha híbrida (trilha tangencial e separação rotativa);
- Inclusão das Classes 7 e 8 com amplo pacote de tecnologia embarcada;
Essas evoluções são diferentes entre as marcas, mas dá para afirmar que hoje a tecnologia de colhedoras atende plenamente a necessidade da pujante agricultura brasileira, e de quebra em muitos países para onde são exportadas.
A colheita é o encerramento de um ciclo produtivo cujo resultado esperado é ter volume de grãos colhidos com qualidade e o suficiente para ter retorno financeiro e poder continuar na atividade de produzir alimento.
Melhores Práticas veem contribuir para esta importante tarefa com dicas preciosas e informações úteis.
TREINAMENTO/CAPACITAÇÃO
O operador e o pessoal da logística que a apoia a atividade de colheita devem ser devidamente treinados para suas funções! A capacitação para colheita deve ser muito bem consistente, pela enorme responsabilidade de finalizar um ciclo de produção com qualidade e pelo valor patrimonial das máquinas e equipamentos.
A QUALIDADE NA COLHEITA – INDICADORES
A qualidade da colheita envolve muitos fatores, que iniciam com a própria cultura, mas cujo ator principal é a própria colhedora, seus recursos e o operador. A exemplo das outras etapas do sistema de produção a colheita precisa de planejamento, logística de apoio e não diferentemente de outros equipamentos as colhedoras exigem MELHORES PRÁTICAS EM manutenção, ajustes ou regulagens e operação para se ter qualidade na colheita!
Para nos ajudar na compilação desta apostila precisamos entender o que se deseja na colheita além de produção abundante, o que chamaríamos de INDICADORES DE QUALIDADE DE COLHEITA, conforme abaixo;
- COLHER TUDO O QUE FOI PLANTADO QUE NASCEU, CRESCEU E AMADURECEU;
- COLHER BAIXO O SUFICIENTE PARA RECOLHER TODAS AS VAGENS, SEM MEXER NO SOLO;
- NÃO DEIXAR NADA PARA TRÁS, SEJA NO CORTE, NA ALIMENTAÇÃO OU NA DEBULHA;
- DEBULHAR SEM CAUSAR PERDAS SEJA POR:
- Grãos Quebrados ou danificados
- Grãos sem debulhar;
- Saída de Grãos de alguma forma;
- SEPARAR OU RECUPERAR OS GRÃOS DAS PALHAS SEM PERDAS;
- LIMPAR TODAS AS IMPURESAS SEM JOGAR GRÃOS FORA;
- TRITURAR A PALHA COMO É DESEJADO E DISTRIBUIR COMPLETAMENTE SOBRE A AREA COLHIDA;
O QUE DEVEMOS FAZER PARA COLHER COM QUALIDADE!
ENTENDIMENTOS:
PRINCIPAIS SISTEMAS E SUB SISTEMAS DE UMA COLHEDORA DE CEREIAS
A Colhedora é uma máquina complexa porque precisa realizar várias funções, para um melhor entendimento foi dividida em Sistemas e estes em Conjuntos para que o Operador possa se situar, compreender e executar corretamente as Melhores Práticas. E através dos Sistemas vamos entender a sua FINALIDADE, FUNÇÕES, PONTOS DE ATENÇÃO OU ALERTAS E A INTERFERÊNCIA DO OPERADOR, segundo recomendam as MELHORES PRÁTICAS!
NORMAS PARA A NOMENCLATURA UTILIZADA PARA MÁQUINAS DE COLHEITA…. ???
- Sistema de corte e de Alimentação
Plataformas de Corte Rígida ou Fixa desenvolvida para colher Arroz e pode ser usada para colher Trigo, Aveia, Linhaça e todas as culturas de inverno!
CONJUNTOS NO SISTEMAS
Caixa de Acionamento, Pontões divisores das Plantas, Barra de Corte Rígida, Mesa Alimentadora, Caracol Centralizador, Canal Elevador ou Embocador;
ALERTAS
O principal ponto de atenção é o estado dos elementos de corte, barras e navalhas. A falta de manutenção, correção ou substituição incorre em um corte irregular e provoca má alimentação. Esse é o problema recorrente que implica em debulha ineficiente, quebra e perdas de grãos.
AO OPERADOR
Inspecione com frequência o estado dos componentes da barra de corte, mesa alimentadora, altura do caracol em relação a mesa.
PERDAS NO CORTE
É comum haver perdas no momento do corte, até mesmo antes, podem ocorrer perdas naturais. Mas as perdas na colheita podem ser minimizadas com boas práticas.
ALERTAS
Descuidos na manutenção, excesso de altura no corte, excesso na rotação e velocidade podem gerar perdas no sistema de corte. Outra perda é dada na forma de descontos de impurezas a existência de terra junto aos grãos entregues. Essa perda por recolhimento de terra é devido a baixa excessiva na altura de corte ou existência de terrões decorrentes de formiga, buraco de tatu ou ainda levantados no momento do plantio.
ATENÇÃO NO CASO DO FEIJÃO
O pé de feijão tem características diferentes da soja, naquele as vagens são mais longas e o caule e os ramos são mais finos e quando chegam ao final do ciclo não suportam o peso das vagens se localizando muito próximas ao solo ou muitas vezes sobre o mesmo, tornando a colheita um tanto desafiadora e exigindo maior atenção. Por esse motivo o índice de perdas no corte na colheita do feijão é elevado e maior em comparação a soja.
ALERTA
Desatenção na colheita do feijão pode afetar a qualidade e aumentar as perdas, comprometendo o resultado financeiro!
AO OPERADOR
Coloque mais atenção quando colher feijão! Veja regulagens específicas no Manual do Operador para colheita do Sr. Feijão.
PROCEDIMENTO PARA VERIFICAR AS PERDAS NO CORTE
Pare a máquina e desligue o sistema de debulha.
- Observe atrás da plataforma a quantidade de grãos no solo.
- Verifique o estado das navalhas, a rotação do molinete deve ser levemente acima da velocidade de deslocamento da máquina.
- A própria velocidade de colheita deve ser condizente com o estado de maturação da cultura, volume de massa que entra e topografia do terreno.
Plataforma Flexível, projetada para colher soja e culturas que exigem corte rente ao solo, também usada para colher as culturas de inverno, menos o milho;
Com o advento do Sistema de Plantio Direto as plataformas tiveram que ser redesenhadas para se adaptar ao sistema para colher rente ao solo, surgindo assim as barras e sistemas flexíveis que copiam a topografia.
CONJUNTOS DA PLATAFORMA DE CORTE FLEXÍVEL
Barra de Corte Flexível, Mesa Alimentadora, Caracol Centralizador, Canal Elevador ou Embocador;
ALERTAS
Ao colher rente ao solo em áreas de pouca cobertura, terra ou pedras podem ser recolhidas pelas navalhas que cortam rente ao solo, causando impurezas no produto ou, no caso de pedras, danificando componentes!
AO OPERADOR
Ajustar altura de corte mais alto respeitado as vagens da primeira inserção. Ajuste o ângulo de corte das navalhas, se tal regulagem for oferecida na máquina. Verifique a pressão dos deslizadores sobre o solo, via controle a partir da Cabina!
Plataforma Drapper (Mesa de Lona e Sem Caracol)
O uso desse conceito de plataformas onde o caracol foi substituído por uma esteira de borracha é recente trazido por empresa Canadense! Esse sistema de alimentação via esteira melhorou a uniformidade de entrada da massa cortada, e com isso melhorou a qualidade e quantidade de produto debulhado ou processado.
ALERTAS
Como as plataformas do tipo Drapper´s são mais largas e mais pesadas é comum ocorrer acidentes por batida contra outros obstáculos. Falhas na Esteira de Alimentação são frequentes. É comum se perceber falta de flexibilidade na barra de corte!
AO OPERADOR
Tomar mais cuidado ao dirigir a colhedora equipada com Plataforma Drapper. Para deslocamentos em estradas use a carreta própria para a Plataforma.
Revise com frequência os ajustes da esteira de lona alimentadora. Atente para os pontos de inspeção e regulagens no Manual do Operador da Plataforma Drapper.
CONJUNTO NO SISTEMAS
Barra de Corte Flexível, Mesa Centralizadora e Alimentadora de Lona, Canal Elevador ou Embocador;
PLATAFORMA PARA MILHO
Como o plantio do milho é feito por linhas e a cultura tem suas características especiais, a sua Colheita é feita também por linhas, por isso a Plataforma é específica para milho. Com algumas adaptações se usa para colher Girassol!
CONJUNTOS DA PLATAFORMA DE MILHO
Pontões separadores, Torpedo e Corrente Alimentadora da espiga, Chapa destacadora da Espiga, Caracol Centralizador e Canal Elevador ou Embocador!
ALERTAS
É comum acontecer os seguintes problemas: Perdas de Espigas inteiras, Espigas cortadas, Arranque do pé inteiro. A causa desses problemas é o mesmo, a abertura das chapas destacadoras, ou muito abertas ou muito fechadas. Devido a variação no tamanho das espigas esse problema é recorrente e exige constantes ajustes.
AO OPERADOR
Apanhe algumas espigas padrão da lavoura e coloque entre as chapas destacadoras. O espaço entre as chapas deve ser a metade da espiga, o suficiente para passar o caule e segurar as espigas.
Muitas vezes as perdas de espigas inteira é devido a altura exagerada da Plataforma, Planta muito madura e tombada. Ou ainda um plantio muito irregular.
Veja no Manual do Operador de como proceder para realizar o ajuste. Algumas marcas oferecem essa possibilidade diretamente da cabine do operador. Busque por velocidade, altura e regulagens adequadas as condições da cultura que está sendo colhida.
A Altura do caracol em relação ao fundo da mesa pode estar muito próximo ou muito afastado. Ajuste para que a folga seja a metade do tamanho da espiga.
- Sistema de Trilha ou Debulha (Cilindro e Côncavo)
Tipo Tangencial (Cilindro de Trilha),
São aquelas que possuem o Cilindro e Côncavo Transversais a máquina. Outra característica é de que possuem Saca-Palhas como Separadores de Grãos das Palhas! Recentemente foi lançada a versão híbrida! Trilha Convencional (Tangencial) e Separação por rotores.
As regulagens da rotação do cilindro debulhador são feitas a partir da cabina e cuja rotação é visualizada no painel na cabine. A Regulagem do Côncavo normalmente é mecânica e a abertura do mesmo é combinado com marcas ou dentes visíveis ao operador.
A rotação do cilindro e abertura do côncavo são regulagens chaves para a qualidade do grão colhido, e a umidade, tamanho do grão e condições da massa vegetal (palhada) são os primeiros parâmetros para iniciar os ajustes da máquina desde a plataforma até a saída da palha.
ALERTAS
O desconhecimento de como executar as regulagens pode comprometer a quantidade e a qualidade do grão a ser colhido. E essa perda e má qualidade pode por em risco resultado econômico da propriedade!
AO OPERADOR
Peça e realize Treinamentos, busque Informações e consulte o Manual do Operador para ter a garantia do domínio das regulagens e operação geral da Colhedora.
A análise das condições do produto que determina o início e sequência da colheita deve ser dada pelos responsáveis e o operador deve estar bem a par do planejamento da colheita. Procurar entender e conhecer essa análise das condições da lavoura para ter facilidade de buscar as regulagens corretas e obter qualidade e quantidade na colheita.
ALERTA: PERDAS NA DEBULHA
As perdas na debulha são normalmente causadas pela regulagem incorreta do cilindro ou no côncavo ou ambos e podem ser identificadas das seguintes formas:
Perdas por Quebra de Grãos (visível), Perdas de Grãos debulhados que são jogados fora (Quantificáveis), e Perdas de Grãos não debulhados que saem preso ao sabugo no caso de milho ou dentro das vagens no caso de soja, feijão, etc… No caso do Trigo e Arroz, grãos não debulhados saem preso aos cachos.
Grãos Quebrados são perdas visíveis e mensurável por medidores. Na entrega nos estabelecimentos receptores os grãos quebrados e as impurezas são descontados em percentual do peso. No beneficiamento são separados e retirados mantendo somente os grãos inteiros.
AO OPERADOR
Ao iniciar a colheita e a cada turno analise o estado do grão a ser colhido (umidade) e faça os ajustes preliminares. Após colher uma porção analise a qualidade do grão colhido dentro do tanque graneleiro ou no mostrador. Verifique se entre as palhas não picadas e no solo atrás da máquina existem grãos presos nas vagens ou sabugo, ou grãos soltos perdidos no chão. Se necessário faça o ajuste fino da rotação do cilindro e/ou da abertura do côncavo.
Tipo Longitudinal (Rotor Axial);
São aquelas que possuem um ou dois Rotores Longitudinais e não possuem Saca-Palhas. A separação da palha e dos grãos é realizada no terço final do Rotor;
Caixa de Pedras
Muitas máquinas possuem uma caixa antes do sistema de trilha ou debulha cujo objetivo é de reter e recolher pedras para evitar que causem maiores danos aos sistemas de debulha;
ALERTA
A falta de limpeza e esvaziamento da Caixa de Pedras pode provocar danos a componentes com altos custos e tempo para trocas!
AO OPERADOR
Antes do Início da jornada diária faça a inspeção e limpeza da Caixa de Pedras. Se estiver trabalhando em regiões de muita pedra, AJUSTE para o MENOR ângulo de ataque das navalhas e SELECIONE a MENOR pressão da mesa alimentadora da PLATAFORMA. Inspecione com mais frequência a Caixa de Pedras!
- Sistema de Separação e Distribuição dos Resíduos
Convencional (Equipada com Saca-Palhas);
As colhedoras com saca-palhas (são os modelos menores, convencionais e mais antigos), são mais simples e mais leves. Demandam menor potência de motor e tem limitações no tamanho das plataformas. Tais limitações estão estabelecidas pela possibilidade de perdas mais altas, e um dos locais dessas perdas pode ser no Sistema de Separação ou Saca-Palhas.
ALERTAS
Excesso de massa colhida e velocidade acima do recomendado são aliados as perdas pelo Sistema de Separação.
AO OPERADOR
Ficar atento ao volume de palhas recolhido para dentro da máquina e a velocidade de colheita. Também ajustes do Côncavo e rotação do Cilindro de debulhas de acordo com a umidade e produção de grãos. Veja com os responsáveis da fazenda os limites de perdas máximo, e os ajustes na velocidade, rotação do cilindro e a abertura do côncavo.
Algumas colhedoras possuem sensores de perdas que refletem de algum forma no monitor. Essas perdas geralmente são da Separação (Saca-Palhas ou Rotor) e das Peneiras (Limpeza). No Saca-Palhas usualmente são poucos os tipos de ajustes para reduzir as perdas a não ser a própria velocidade de colheita que influi no volume de palhas dentro da máquina, cujo aumento dificulta a recuperação dos grãos que escaparam da debulha junto com a palha.
Cilindro Rotativo quando Equipada com Rotor Axial – AXIAL FLOW
Rotor Axial é aquele longitudinal ao comprimento da máquina, sendo debulha e separação juntos no mesmo corpo com barras raspadoras diferentes. A principal diferença é a maior capacidade de debulha o que permite reduzir a rotação e com isso obter mais qualidade na forma de grãos inteiros. São excelentes para colher feijão e milho!
ALERTAS
São percebidas palhas excessivamente picadas, grãos quebrados, ou ainda ´perdas no cacho, no sabugo ou nas vagens.
AO OPERADOR
Regular a Abertura do Côncavo e Rotação do Cilindro. Veja no quadro Falhas e Possíveis Causas no Manual do Operador e execute os ajustes necessários conforme orientação do fabricante da Colhedora!
Sensores de Perdas
A maioria das Colhedoras Axiais são equipadas com Sensores de Perdas, importante dispositivo de auxílio a colheita. Respeitar o índice de Perdas máximo definido pelos responsáveis é fundamental para assegurar a Qualidade na Colheita!
ALERTA
Sensores descalibrados ou sujos são causadores de interpretações equivocadas de indicadores de qualidade de colheita via índice de perdas.
Assegure que os Sensores de Perdas estejam calibrados e limpos. Busque orientações no Manual do Operador de como proceder para calibrar o sensor!
Picador ou Distribuidor de Palhas
Esses conjuntos tem a importante tarefa de processar a palha e recolocar em toda a largura de corte, facilitando sua decomposição e proteção do solo.
ALERTAS
As condições e estado da palha tem muito a dizer sobre a qualidade da colheita! Palhas acumuladas e parte do solo não coberto. Pode ser excesso de vento lateral ou falta de ajustes. Proceda as regulagens conforme manual do operador! Palhas muito inteiras ou muito picadas, veja em regulagens no Sistema de Separação!
AO OPERADOR
Observe com certa frequência as palhas, os grãos colhidos e o solo procurando pelos indicadores de qualidade de colheita em cada um desses locais! Faça os ajustes e regulagens cabíveis! Na dificuldade consulte o Manual e busque ajuda e aprovação dos seus indicadores a qualidade do grão colhido, na distribuição e tamanhos das palhas e nas perdas no solo!
- Sistema de Limpeza
Este é o sistema responsável pela qualidade visual do grão! É também um sistema de muita atenção para garantir que a maioria dos grãos colhidos sejam armazenados, com um mínimo de perdas!
CONJUNTOS DO SISTEMA DE LIMPEZA!
4.1 – PENEIRA SUPERIOR
4.2 PENEIRA INFERIOR
4.3 BANDEJÃO
4.4 RETRILHA
Peneiras e Bandejão ou “Peneirão”
CONJUNTOS DO SISTEMA DE LIMPEZA
Ventilador, Peneira Superior, Peneira Inferior, Retrilha, Sensores de Perdas e Regulagens!
O sistema de limpeza é um dos principais sistemas da Colhedora poque é responsável pela qualidade do grão colhido pelas perdas de grãos debulhados!
ALERTA
Muita sujeira no graneleiro de grãos e muitas perdas no solo!
AO OPERADOR
Verifique as regulagens das peneiras, como também a rotação do ventilador que pode estar acima do necessário!
Sensores de Perdas
Ventilador
Sistema de Retrilha
- Sistema de Transporte e Armazenagem
Elevadores
Monitores de Rendimento e de Umidade
Reservatório
Sensor de Enchimento
Cobertura do Reservatório
- Sistema de Descarga
Acionamento da Descarga
Tubo de Descarga
Sensores de Aproximação
- Sistema de Transmissão
Mecânica
Hidrostática
- Cabina
Acessos e Pontos de Atenção a Segurança
Comandos e Controles
Monitores
Calibrações
REVISÃO GERAL
Devemos sempre estar atentos aos detalhes: realizar a revisão da colhedora sempre antes de efetuar as colheitas, a troca de peças que estejam com vida útil condenada e efetuar a melhor regulagem do equipamento conforme a cultura, a umidade do grão e, claro, sempre sem pressa porque a colhedora precisa de um tempo para processar o corte, trilha, separação e limpeza. As perdas que ocorrem durante o processo de colheita vão afetar diretamente o lucro da lavoura de soja.
PRIMEIROS PONTOS DE ATENÇÃO
Antes de iniciar o trabalho da colheita atente para o seguinte:
- Assegure-se que a máquina tenha recebido a devida manutenção e revisão. Falaremos isso em capítulo dedicado!
- Abastecimento e Inspeção de Rotina:
O PROBLEMA
Pela diferença de temperatura entre a superfície do Reservatório de Combustível com a do meio ambiente, que possui umidade, provoca a condensação de água nessa superfície por atrair umidade enquanto esfria!
Água misturada com combustível pode causar sérios danos ao motor e seus sistemas!
AO OPERADOR OU RESPONSÁVEL
As Melhores Práticas recomendam que o abastecimento realizado no final da jornada, uma vez que o motor, reservatório e máquina estão aquecidos, evitaria condensação de água dentro do reservatório de combustível, se permanecesse vazio!
Já a Inspeção de Rotina é desejável que se faça pela manhã antes de se iniciarem a colheita porque algo pode ter acontecido na noite durante o repouso!
- Itens de Segurança no seu local e de fácil identificação e acesso;
- Haverá um capítulo sobre SEGURANÇA
- Mantenha o Manual do Operador ou do Proprietário sempre ao alcance da mão;
- Revise os Pneus/Rodados devem estar em excelente estado e devidamente calibrados;
- Assegure que a lubrificação seja feita conforme instruções no manual da máquina;
PERDAS NA COLHEITA
A colheita é uma das principais etapas no ciclo produtivo, principalmente por poder influenciar na produtividade, caso as regulagens da colhedora não estejam adequadas. A colheita da soja na região centro-oeste do Brasil normalmente é realizada com tecnologia avançada. No entanto, ainda se observam colhedoras mais antigas, que podem causar perdas significativas durante o processo de colheita. O objetivo deste trabalho foi quantificar as perdas na colheita de soja de duas máquinas colhedoras com idades diferentes numa lavoura comercial. Para tanto foram utilizadas duas colhedoras de fluxo tangencial, combinadas com plataformas tipo molinete, uma com ano de fabricação 1989 (New Holland 4040) e outra 2001 (John Deere 1175). As perdas foram mensuradas pelos métodos volumétrico e gravimétrico. As coletas foram feitas em três posições de colheita: a) pré colheita, b) plataforma de corte e c) total. A partir desses dados foram calculadas as perdas nos mecanismos de trilha, separação e limpeza. Os resultados mostram que a perda total média foi de 3,23 sacos por hectare, sendo 1,24% de perda na pré-colheita, 53,90% na plataforma de corte e 44,86% na trilha, separação e limpeza das colhedoras. Não há diferença significativa nas perdas totais entre as colhedoras com idades diferentes. O método gravimétrico é mais preciso para avaliar as perdas de soja. PALAVRAS-CHAVE: Colhedora de grãos, Perdas, Soja
ALERTA
Durante a colheita é normal que ocorram algumas perdas. Porém, é necessário que estas sejam sempre reduzidas a um mínimo para que o lucro seja maior. A percentagem de perdas pode ser relacionada à má regulagem da máquina, principalmente no mecanismo de corte e alimentação. Porém, o efeito desses fatores pode ser minimizado pela adoção de práticas de manejo que fazem com que as plantas de soja tenham o melhor aproveitamento possível. Hoje podemos ter perdas significativas na nossa colheitadeira se não observarmos alguns detalhes. Estas perdas ocorreram na plataforma de corte, nos mecanismos de trilha, separação e limpeza dos grãos.
AO OPERADOR
A velocidade de trabalho recomendada para uma colhedora de soja é determinada em função da produtividade da cultura e da capacidade admissível de manusear toda a massa que é colhida junto com o grão. Ao tomar a decisão de aumentar ou diminuir a velocidade não se deve preocupar somente com a capacidade de trabalho da colhedora, mas verificar se os níveis toleráveis de perdas estão sendo respeitados. A maioria das perdas relacionadas à má regulagem da máquina ocorre no mecanismo de corte e alimentação.
PONTOS DE ATENÇÃO
Deve ser dada atenção especial ao posicionamento do molinete em relação à barra de corte e à velocidade do molinete. Se esta for excessiva, ocorrerão muitos impactos sobre as plantas, resultado em quebra dos ponteiros com a consequente queda de vagens e grão no chão. Em termos práticos, a velocidade do molinete deve ser um pouco superior à de deslocamento da colhedora em operação. Com isso, tem-se a impressão que o molinete puxa a colhedora e patina suavemente sobre as plantas de soja. Em termos percentuais, a rotação do molinete deve ser correspondente de 15% a 20% acima da velocidade da colhedora. O estado de conservação da barra de corte e de seus componentes ativos (navalha e contra navalhas) também não deve ser negligenciado. Facas cegas e dedos das contra navalhas frouxos diminuem a ação de corte e aumentam a vibração das plantas, promovendo abertura de vagens e quedas de grãos fora da plataforma. Com relação às perdas durante a trilha, estas podem ocorrer no cilindro batedor ou nas peneiras que separam os grãos da palha. Essas perdas são mínimas quando comparadas com aquelas da plataforma de corte. Não podemos deixar de destacar, além da umidade do grão colhido, a falta de manutenção da serra, navalhas quebradas, folga da barra de corte, efetuar a substituição e os ajustes necessários, já no molinete com aceleração muito alta. O molinete: a dica é que trabalhe com 20% superior de aceleração à velocidade da máquina. Estas situações aumentam consideravelmente o atrito das plantas e dos grãos com a plataforma ocasionando grandes perdas.
MANUTENÇÃO E INSPEÇÃO DE ROTINA DA COLHEDORA
Por executarem várias funções ao mesmo tempo em que se movem, as colhedoras são máquinas complexas reunindo praticamente toda os tipos de sistemas conhecidos. O projeto integra Sistemas Hidráulicos, Mecânicos, Elétricos, Eletrônicos e de Comunicação, o que as transformaram em produto de elevado valor agregado, sendo que a manutenção, cuidados e inspeção de rotina sejam atividades obrigatórias!
ALERTA
A falta de manutenção e inspeção diária incorrem em sérios riscos de paradas ou falhas por vários possíveis motivos e com elevados custos.
O fabricante de cada Colhedora informa em seus manuais do operador ou do proprietário o que fazer, onde e a que frequências
OPERADOR
Consulte o Manual, solicite ajuda se precisar entender melhor as recomendações e alerte os responsáveis pela manutenção de rotina!
O QUE FAZER NA INSPEÇAO DE ROTINA DIÁRIA
Usualmente o Manual DO Operador/Proprietário consta os pontos críticos em cada sistema para ser verificado. Independente do Manual, faça essa inspeção VISUAL sempre que tiver oportunidade, principalmente nos seguintes sistemas:
Estado das Navalhas de Corte;
Molas em Geral;
Correias e Polias Tensoras
Peneiras, Picador de Palhas
ALERTAS
Pelo trabalho ser em condições muito severas e muitos sistemas trabalhado em conjunto não é raro componentes estarem trabalhando em condições precárias, desregulados, fora do lugar, frouxos ou até mesmo perdidos.
A não observação dessa PRÁTICA da inspeção de rotina põe em risco o trabalho de colheita.
ATENÇÃO OPERADOR
A COLHEDORA E A AGRICULTURA DE PRECISÃO
SENSORES E DISPOSITIVOS DE UMA COLHEDORA DE GRÃOS
Em uma colhedora de grãos utilizada na agricultura de precisão é empregado diversos recursos eletrônicos com alta tecnologia, para a captação de dados e a para sua interpretação. Estes recursos estão sendo cada vez mais explorados e desenvolvidos, a fim de auxiliar e aumentar a produtividade das colheitas. Dentre os principais componentes utilizados nessas máquinas estão: monitores, que fornecem informações ininterruptas e instantâneas, de rendimento, perda, umidade, área trabalhada, mapas de produtividade, entre outras informações; que são alimentados de dados através de vários sensores eletrônicos distribuídos pelos sistemas da máquina.
Antigamente as colheitadeiras mecânicas de grãos já possuíam alguns tipos de sensores, mais rudimentares, por essas máquinas não possuírem um sistema elétrico que comportasse muitos dispositivos eletrônicos, elas possuíam os componentes eletrônicos essenciais para o seu funcionamento, coo exemplo um sensor de rotação nos eixos. Apesar de rudimentares, esses sensores e dispositivos instalados nessas máquinas, já auxiliavam na colheita dos grãos, alguns deles podem ser encontrados ainda nas mais sofisticadas colhedoras da atualidade. Um outro exemplo disso pode ser mencionado os sistemas de catracas instalados nas diversas polias e correias existentes nos sistemas mecânicos das colheitadeiras, tanto nas mais rudimentares e simples como nas mais sofisticadas e avançadas, tecnologicamente. Outro sistema que ainda é encontrado em várias colheitadeiras da atualidade é o sistema de coleta de pedras. Apesar de já existir vários sensores para evitar a entrada de pedras no cilindro das máquinas, a caixa-de-pedra é encontrada em muitas máquinas com altas tecnologias, por se tratar de um sistema que evita danos maiores nos outros sistemas da máquina.
DESLOCAMENTOS EM VIAS PÚBLICAS
Existe uma tendência de arrendamento e aquisição de lavouras não contínuas, exigindo constantes deslocamentos o que requer atenção especial pela segurança pessoal, dos outros veículos e das máquinas agrícolas em movimentação! O proprietário e gestores das Colheitas responsáveis pelas Máquinas precisam passar as orientações aos Operadores, cuidar se as máquinas estão com os decais e iluminação em dia, se os batedores estão a postos.
No Brasil a legislação de Trânsito estabelece as regras para os veículos, e também para máquinas Agrícolas. O Operador deve procurar se orientar com relação a essas regras.
INÍCIO DOS TRABALHOS
A PRIMEIRA INFORMAÇÃO AO OPERADOR
Os Gestores devem orientar para a distribuição das máquinas nas frentes de colheita, quando for o caso de mais do que uma máquina em trabalho no mesmo talhão. Assim também com relação ao posicionamento dos Veículos responsáveis pela logística do produto colhido.
Os principais fatores que determinam o início de colheita são a umidade do produto a ser colhido e a data de início do plantio da cultura seguinte. As vezes este último fator força acolher o produto com a umidade mais alta do que gostaria. A umidade do grão é a primeira informação que o operador precisa ter antes de começara a regular a máquina para colher.
ALERTA
Caso a umidade não for levada e consideração para regular a Colhedora, vários problemas poderão surgir principalmente no que se refere a perdas, danos nas sementes e impurezas!